SMT folosește o soluție convențională de analiză și soluție de sudură cu pastă de lipit prin refluxarea aerului (2023 Essence Edition), meritați!
1 Introducere

În ansamblul plăcii de circuite, pasta de lipit este imprimată mai întâi pe placa de lipire a plăcii de circuite, apoi sunt fixate diverse componente electronice. În cele din urmă, după cuptorul de reflow, margelele de staniu din pasta de lipit sunt topite și toate tipurile de componente electronice și placa de lipit a plăcii de circuite sunt sudate împreună pentru a realiza asamblarea submodulelor electrice. tehnologia de montare în suprafață (sMT) este din ce în ce mai utilizată în produsele de ambalare de înaltă densitate, cum ar fi pachetul la nivel de sistem (siP), dispozitivele ballgridarray (BGA) și chipul power bare, pachetul pătrat plat fără pin (quad aatNo-lead, denumit QFN). ) dispozitiv.
Datorită caracteristicilor procesului și materialelor de sudare a pastei de lipit, după sudarea prin reflow a acestor dispozitive cu suprafață mare de lipit, vor exista găuri în zona de sudare a lipitului, care vor afecta proprietățile electrice, proprietățile termice și proprietățile mecanice ale produsului Performanța și chiar duce la defectarea produsului, prin urmare, pentru a îmbunătăți pasta de lipit, cavitatea de sudare prin reflow a devenit un proces și o problemă tehnică care trebuie rezolvată, unii cercetători au analizat și studiat cauzele a cavității de sudură cu bile de lipit BGA și a furnizat soluții de îmbunătățire, lipsește o zonă de sudare a procesului de sudare prin refluxare a pastei de lipit convențional cu QFN mai mare de 10 mm2 sau o zonă de sudare mai mare de 6 mm2 soluția de așchii goale a lui.
Utilizați sudarea Preformsolder și sudarea în cuptor cu reflux în vid pentru a îmbunătăți orificiul de sudare. Lipirea prefabricată necesită echipament special pentru a puncta fluxul. De exemplu, cipul este decalat și înclinat serios după ce cipul este plasat direct pe lipitura prefabricată. Dacă cipul de montare a fluxului este reflow și apoi punct, procesul este crescut cu două reflow, iar costul lipiturii prefabricate și al materialului de flux este mult mai mare decât pasta de lipit.
Echipamentul de reflux de vid este mai scump, capacitatea de vid a camerei independente de vid este foarte scăzută, performanța costurilor nu este ridicată, iar problema stropirii cu staniu este gravă, ceea ce este un factor important în aplicarea de înaltă densitate și cu pas mic. produse. În această lucrare, bazată pe procesul convențional de sudare a pastei de lipit, este dezvoltat și introdus un nou proces de sudare secundară pentru a îmbunătăți cavitatea de sudare și pentru a rezolva problemele legate de lipire și fisurarea etanșării din plastic cauzate de cavitatea de sudare.
2 Pastă de lipit imprimare cavitate de sudare prin reflow și mecanism de producție
2.1 Cavitatea de sudare
După sudarea prin reflow, produsul a fost testat sub raze X. S-a constatat că găurile din zona de sudare cu o culoare mai deschisă se datorează lipirii insuficiente în stratul de sudură, așa cum se arată în Figura 1.
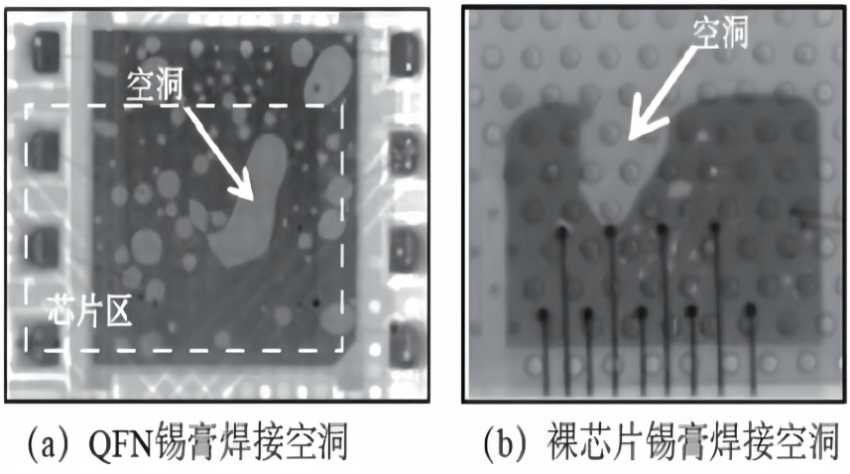
Detectarea cu raze X a găurii bulei
2.2 Mecanismul de formare a cavităţii de sudare
Luând ca exemplu pasta de lipit sAC305, compoziția și funcția principală sunt prezentate în Tabelul 1. Fluxul și margelele de staniu sunt lipite împreună în formă de pastă. Raportul de greutate dintre lipirea cu staniu și flux este de aproximativ 9:1, iar raportul de volum este de aproximativ 1:1.
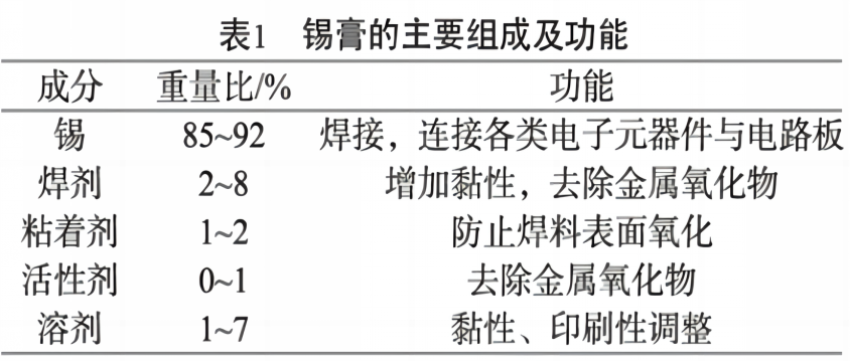
După ce pasta de lipit este imprimată și montată cu diverse componente electronice, pasta de lipit va trece prin patru etape de preîncălzire, activare, reflux și răcire atunci când trece prin cuptorul cu reflux. Starea pastei de lipit este, de asemenea, diferită cu temperaturi diferite în diferite etape, așa cum se arată în Figura 2.
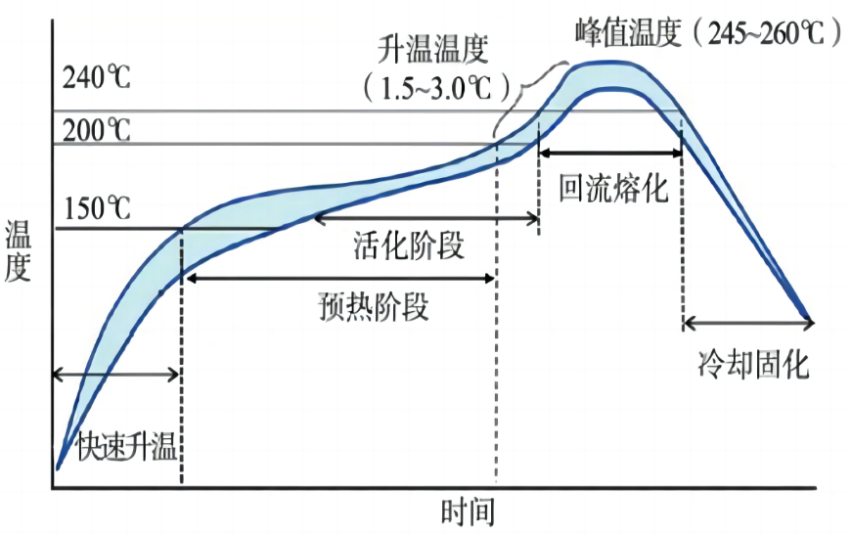
Referință de profil pentru fiecare zonă de lipire prin reflow
În etapa de preîncălzire și activare, componentele volatile din fluxul din pasta de lipit vor fi volatilizate în gaz atunci când sunt încălzite. În același timp, se vor produce gaze atunci când oxidul de pe suprafața stratului de sudură este îndepărtat. Unele dintre aceste gaze se vor volatiliza și vor lăsa pasta de lipit, iar granulele de lipit vor fi strâns condensate din cauza volatilizării fluxului. În etapa de reflux, fluxul rămas în pasta de lipit se va evapora rapid, margelele de staniu se vor topi, o cantitate mică de gaz volatil de flux și cea mai mare parte a aerului dintre margelele de staniu nu va fi dispersat în timp, iar reziduul din staniul topit și sub tensiunea staniului topit sunt structura sandwich de hamburger și sunt prinse de placa de lipire a plăcii de circuite și de componentele electronice, iar gazul învelit în staniul lichid este dificil de scăpat numai prin flotabilitatea în sus. Timpul de topire superior este foarte scurt. Când staniul topit se răcește și devine staniu solid, apar pori în stratul de sudură și se formează găuri de lipit, așa cum se arată în Figura 3.
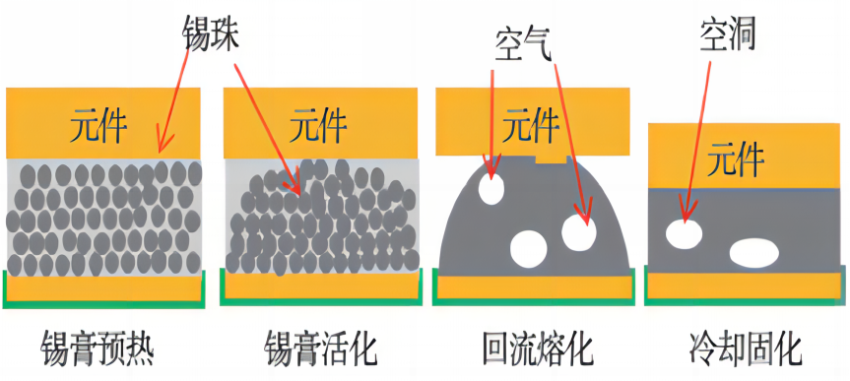
Diagrama schematică a golurilor generate de sudarea prin reflow cu pastă de lipit
Cauza principală a cavității de sudare este că aerul sau gazul volatil învelit în pasta de lipit după topire nu este complet descărcat. Factorii de influență includ materialul de pastă de lipit, forma de imprimare a pastei de lipit, cantitatea de imprimare a pastei de lipit, temperatura de reflux, timpul de reflux, dimensiunea sudurii, structura și așa mai departe.
3. Verificarea factorilor de influență ai găurilor de sudură prin reflow tipărire a pastei de lipit
Testele QFN și bare chip au fost utilizate pentru a confirma principalele cauze ale golurilor de sudură prin reflow și pentru a găsi modalități de îmbunătățire a golurilor de sudură prin reflow imprimate cu pasta de lipit. Profilul produsului de sudare QFN și pastă de lipire cu așchii goale este prezentat în Figura 4, dimensiunea suprafeței de sudare QFN este de 4,4 mm x 4,1 mm, suprafața de sudare este strat cositorit (100% staniu pur); Dimensiunea de sudare a cipului gol este de 3,0 mm x 2,3 mm, stratul de sudură este un strat bimetalic de nichel-vanadiu pulverizat, iar stratul de suprafață este vanadiu. Placa de sudură a substratului a fost cu scufundare în aur de nichel-paladiu, iar grosimea a fost de 0,4μm/0,06μm/0,04μm. Se folosește pasta de lipit SAC305, echipamentul de imprimare a pastei de lipit este DEK Horizon APix, echipamentul cuptorului cu reflux este BTUPyramax150N, iar echipamentul cu raze X este DAGExD7500VR.
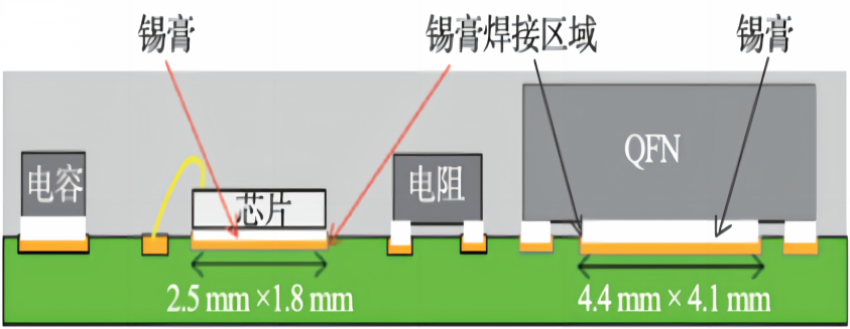
QFN și desene de sudare cu așchii goale
Pentru a facilita compararea rezultatelor testelor, sudarea prin reflow a fost efectuată în condițiile din Tabelul 2.
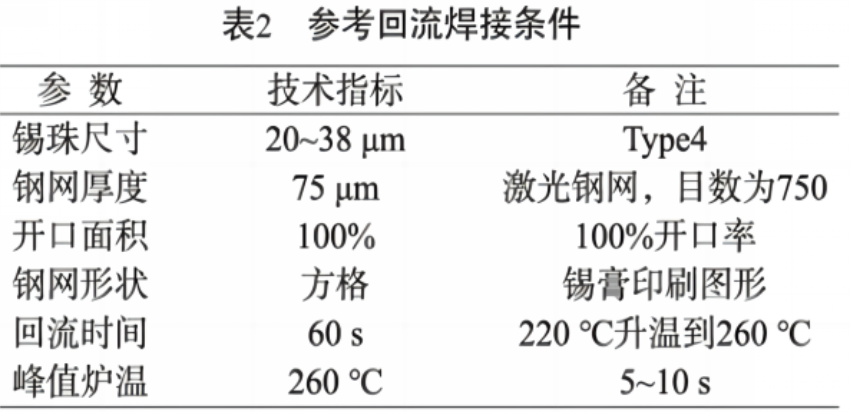
Tabel de stare de sudare prin reflow
După ce s-au terminat montarea la suprafață și sudarea prin reflow, stratul de sudură a fost detectat prin raze X și s-a constatat că există găuri mari în stratul de sudură în partea de jos a QFN și așchii goale, așa cum se arată în Figura 5.
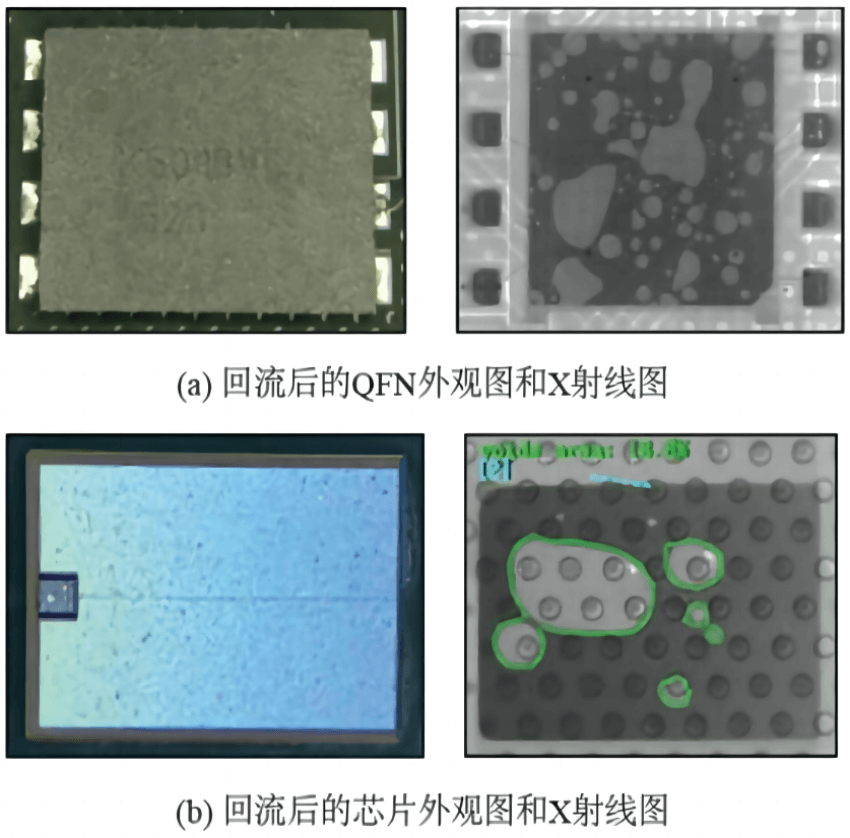
QFN și Holograma Chip (Raze X)
Deoarece dimensiunea mărgelelor de staniu, grosimea ochiului de oțel, rata de deschidere, forma ochiului de oțel, timpul de reflux și temperatura maximă a cuptorului vor afecta toate golurile de sudură prin reflow, există mulți factori care influențează, care vor fi verificați direct prin testul DOE și numărul de experimente. grupurile vor fi prea mari. Este necesar să se verifice rapid și să se determine principalii factori de influență prin testul de comparare a corelației și apoi să se optimizeze în continuare principalii factori de influență prin DOE.
3.1 Dimensiunile orificiilor de lipit și ale granulelor de tablă de pastă de lipit
Cu testul tip 3 (dimensiunea granulelor 25-45 μm) SAC305 cu pastă de lipit, celelalte condiții rămân neschimbate. După refluxare, găurile din stratul de lipit sunt măsurate și comparate cu pasta de lipit de tip 4. Se constată că găurile din stratul de lipit nu sunt semnificativ diferite între cele două tipuri de pastă de lipit, ceea ce indică faptul că pasta de lipit cu dimensiuni diferite ale granulelor nu are o influență evidentă asupra găurilor din stratul de lipit, ceea ce nu este un factor de influență, după cum se arată în fig. 6 După cum se arată.
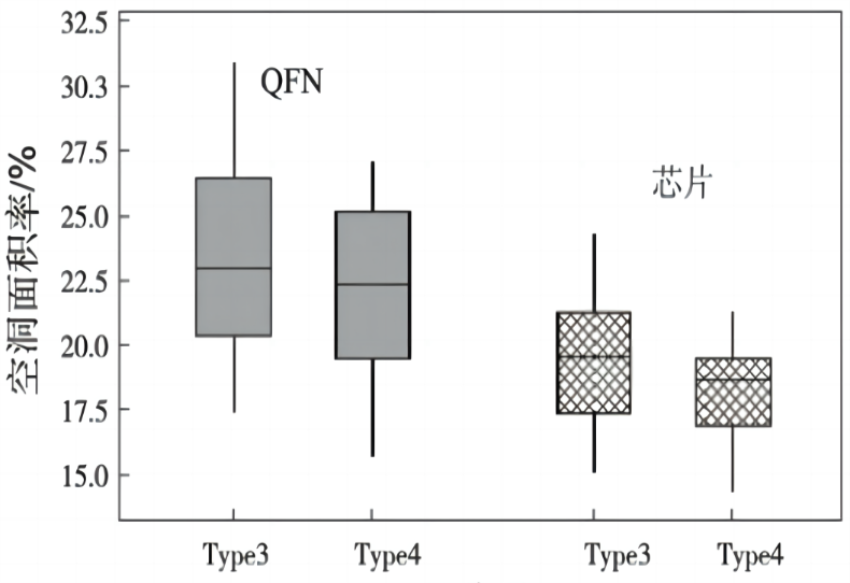
Comparația găurilor metalice de pulbere de staniu cu diferite dimensiuni ale particulelor
3.2 Grosimea cavitatii de sudura si plasa de otel imprimata
După refluxare, aria cavității stratului sudat a fost măsurată cu plasa de oțel imprimată cu grosimea de 50 μm, 100 μm și 125 μm, iar alte condiții au rămas neschimbate. Sa constatat că efectul diferitelor grosimi ale plasei de oțel (pastă de lipit) asupra QFN a fost comparat cu cel al plasei de oțel imprimat cu grosimea de 75 μm Pe măsură ce grosimea plasei de oțel crește, zona cavității scade treptat lent. După atingerea unei anumite grosimi (100μm), zona cavității se va inversa și începe să crească odată cu creșterea grosimii plasei de oțel, așa cum se arată în Figura 7.
Acest lucru arată că atunci când cantitatea de pastă de lipit crește, staniul lichid cu reflux este acoperit de cip, iar evacuarea aerului rezidual este îngustă doar pe patru laturi. Atunci când cantitatea de pastă de lipit este schimbată, evacuarea aerului rezidual este, de asemenea, crescută, iar explozia instantanee de aer învelit în staniu lichid sau gaz volatil care scapă staniu lichid va face ca staniul lichid să stropească în jurul QFN și cip.
Testul a constatat că, odată cu creșterea grosimii plasei de oțel, explozia bulei cauzată de scăparea aerului sau a gazului volatil va crește, de asemenea, și probabilitatea stropirii cu staniu în jurul QFN și cip va crește, de asemenea, în mod corespunzător.
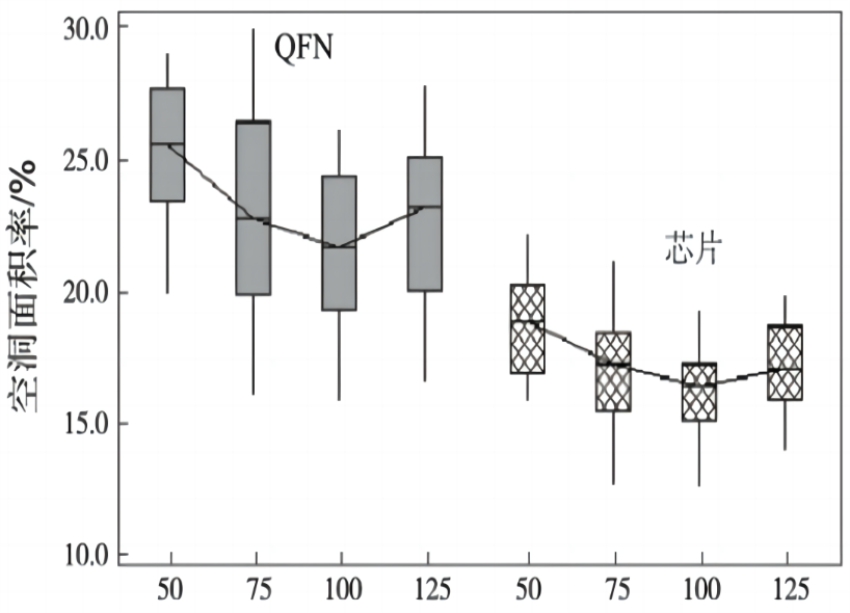
Comparația găurilor din plasa de oțel de diferite grosimi
3.3 Raportul suprafeței dintre cavitatea de sudare și deschiderea plasei de oțel
Plasa de oțel imprimată cu rata de deschidere de 100%, 90% și 80% a fost testată, iar alte condiții au rămas neschimbate. După refluxare, aria cavității stratului sudat a fost măsurată și comparată cu plasa de oțel imprimată cu o rată de deschidere de 100%. S-a constatat că nu a existat nicio diferență semnificativă în cavitatea stratului sudat în condițiile ratei de deschidere de 100% și 90% 80%, așa cum se arată în Figura 8.
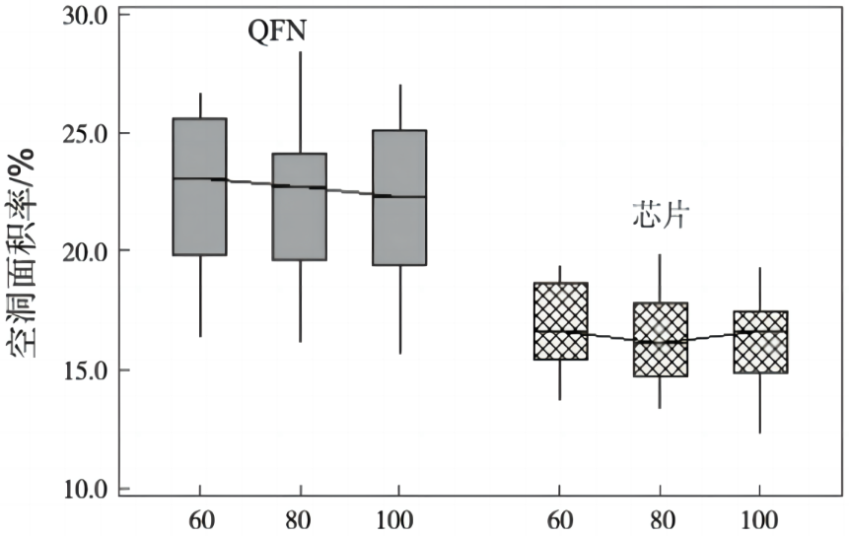
Compararea cavităților diferitelor zone de deschidere ale diferitelor plase de oțel
3.4 Cavitatea sudata si forma ochiului de otel imprimat
Cu testul formei de imprimare a pastei de lipit a benzii b și a grilei înclinate c, celelalte condiții rămân neschimbate. După refluxare, aria cavității stratului de sudură este măsurată și comparată cu forma de imprimare a rețelei a. Se constată că nu există o diferență semnificativă în cavitatea stratului de sudură în condițiile grilei, benzii și grilei înclinate, așa cum se arată în Figura 9.
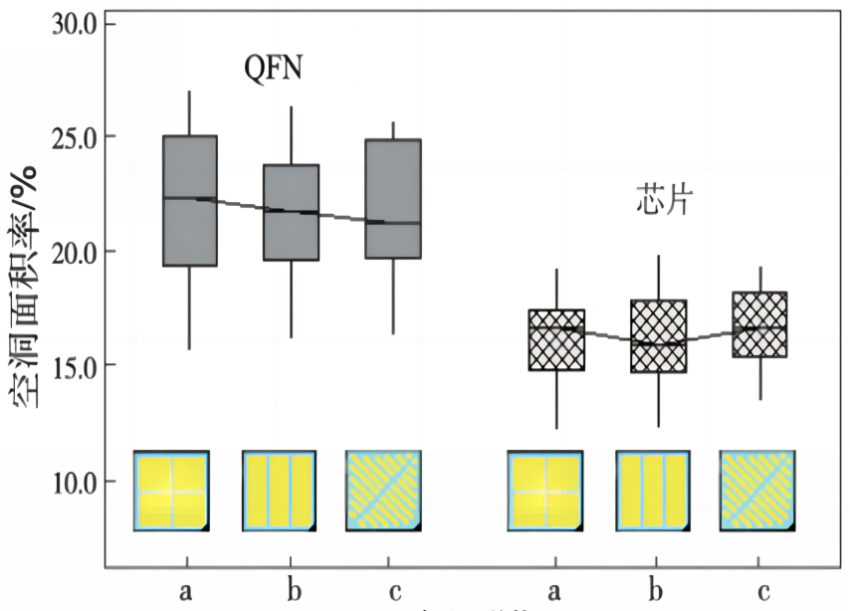
Comparația găurilor în diferite moduri de deschidere a plasei de oțel
3.5 Cavitatea de sudare și timpul de reflux
După testarea timpului de reflux prelungit (70 s, 80 s, 90 s), alte condiții rămân neschimbate, gaura din stratul de sudură a fost măsurată după reflux și, comparativ cu timpul de reflux de 60 s, s-a constatat că odată cu creșterea timpul de reflux, aria găurii de sudare a scăzut, dar amplitudinea de reducere a scăzut treptat odată cu creșterea timpului, așa cum se arată în Figura 10. Acest lucru arată că în în cazul unui timp de reflux insuficient, creșterea timpului de reflux este propice pentru revărsarea completă a aerului învelit în staniu lichid topit, dar după ce timpul de reflux crește până la un anumit timp, aerul învelit în staniu lichid este dificil de revărsat din nou. Timpul de reflux este unul dintre factorii care afectează cavitatea de sudare.
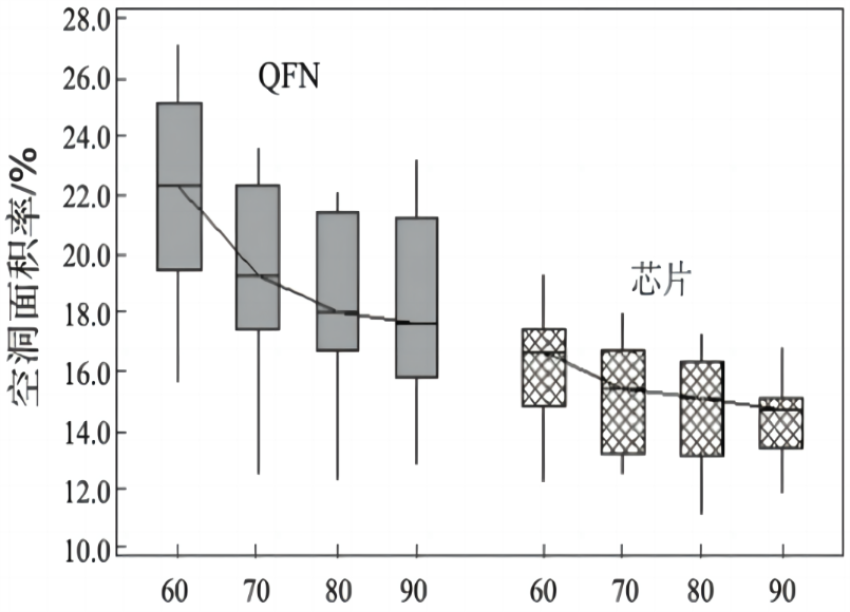
Comparație nulă a diferitelor durate de timp de reflux
3.6 Cavitatea de sudare și temperatura maximă a cuptorului
Cu testul de temperatură maximă a cuptorului de 240 ℃ și 250 ℃ și alte condiții neschimbate, aria cavității stratului sudat a fost măsurată după refluxare și, în comparație cu temperatura maximă a cuptorului de 260 ℃, s-a constatat că în diferite condiții de temperatură de vârf a cuptorului, cavitatea stratul sudat de QFN și cip nu s-a schimbat semnificativ, așa cum se arată în Figura 11. Acesta arată că temperatura de vârf diferită a cuptorului nu are un efect evident asupra QFN și a găurii din stratul de sudură al așchii, ceea ce nu este un factor de influență.
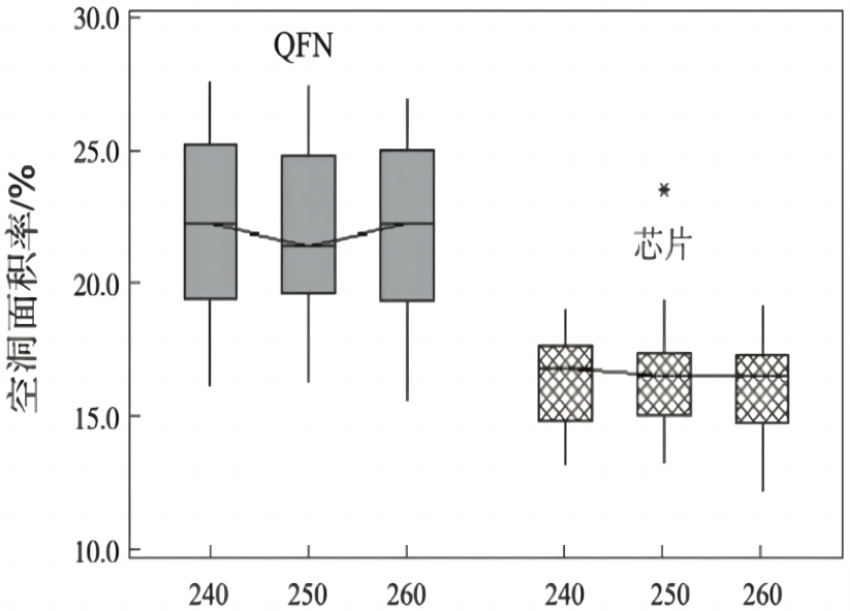
Comparație nulă a diferitelor temperaturi de vârf
Testele de mai sus indică faptul că factorii semnificativi care afectează cavitatea stratului de sudură a QFN și a așchii sunt timpul de reflux și grosimea oțelului.
4 Imbunatatirea cavitatii de sudare prin reflow prin pasta de lipit
Test 4.1DOE pentru a îmbunătăți cavitatea de sudare
Orificiul din stratul de sudură de QFN și cip a fost îmbunătățit prin găsirea valorii optime a principalilor factori de influență (timpul de reflux și grosimea oțelului). Pasta de lipit a fost SAC305 tip4, forma ochiului de oțel a fost tip grilă (grad de deschidere 100%), temperatura maximă a cuptorului a fost de 260 ℃ și alte condiții de testare au fost aceleași cu cele ale echipamentului de testare. Testul DOE și rezultatele au fost prezentate în Tabelul 3. Influența grosimii ochiului de oțel și a timpului de reflux asupra QFN și a găurilor de sudare a așchiilor sunt prezentate în Figura 12. Prin analiza interacțiunii principalelor factori de influență, se constată că folosind grosimea ochiului de oțel de 100 μm iar timpul de reflux de 80 s poate reduce semnificativ cavitatea de sudare a QFN și a cipului. Rata cavității de sudare a QFN este redusă de la maxim 27,8% la 16,1%, iar rata cavității de sudare a așchii este redusă de la maxim 20,5% la 14,5%.
În cadrul testului, 1000 de produse au fost produse în condiții optime (grosimea plasei de oțel de 100 μm, timp de reflux de 80 s), iar rata cavității de sudare de 100 QFN și cip a fost măsurată aleatoriu. Rata medie a cavității de sudare a QFN a fost de 16,4%, iar rata medie a cavității de sudare a așchii a fost de 14,7% Rata cavității de sudare a așchiului și a așchii este în mod evident redusă.
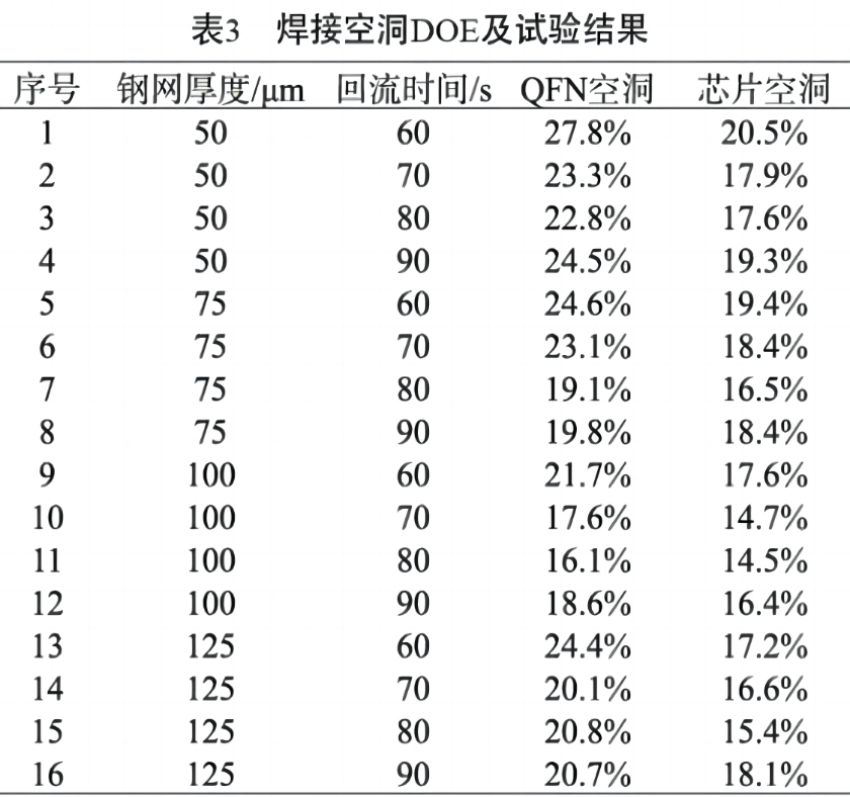
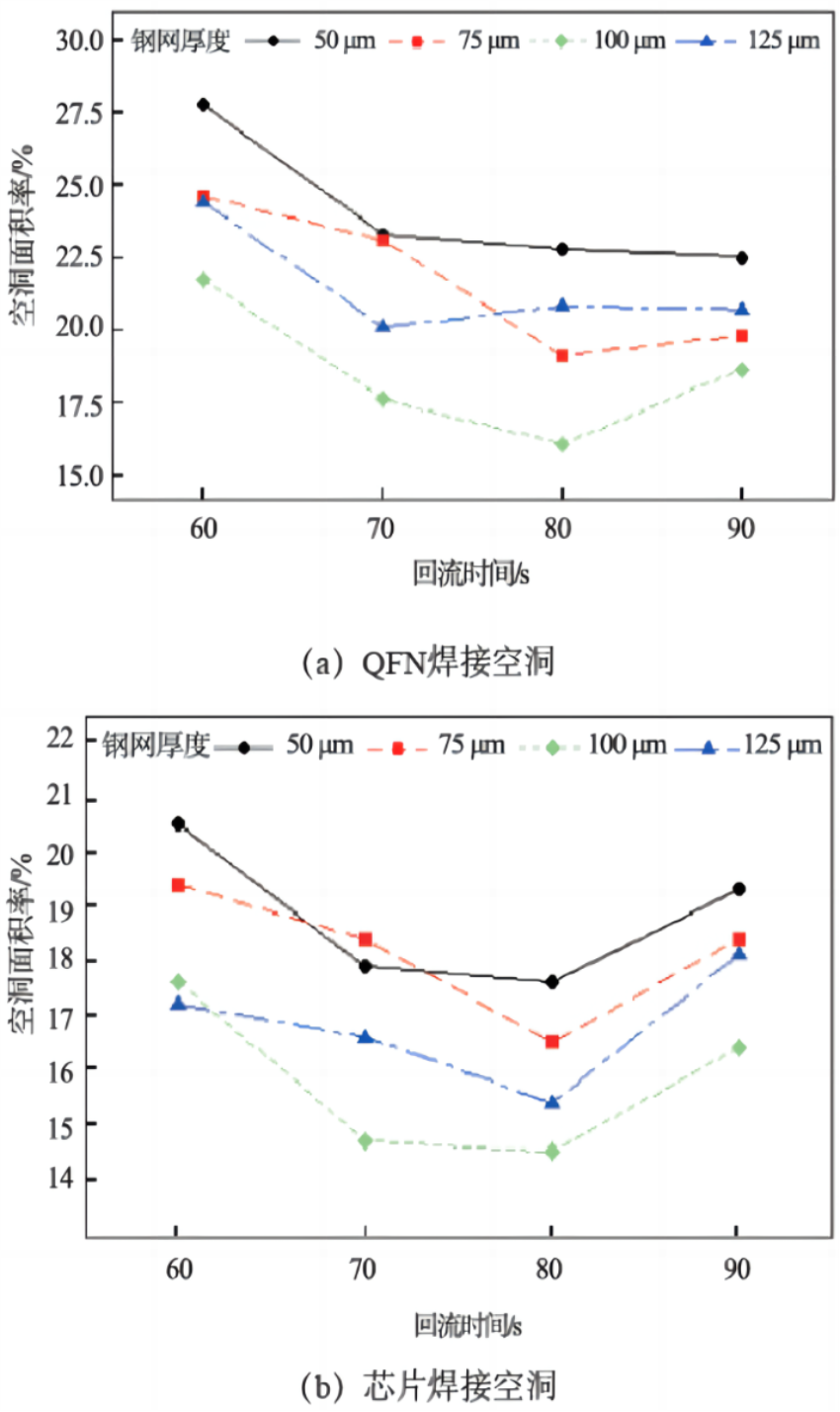
4.2 Noul proces îmbunătățește cavitatea de sudare
Situația reală de producție și testul arată că atunci când zona cavității de sudare din partea inferioară a așchii este mai mică de 10%, problema de fisurare a poziției cavității așchii nu va apărea în timpul lipirii și turnării plumbului. Parametrii procesului optimizați de DOE nu pot îndeplini cerințele de analiză și soluționare a găurilor din sudarea convențională prin reflow cu pastă de lipit, iar rata suprafeței cavității de sudare a cipului trebuie redusă și mai mult.
Deoarece așchiul acoperit pe lipit împiedică scăparea gazului din lipire, rata orificiilor din partea inferioară a cipului este redusă și mai mult prin eliminarea sau reducerea gazului acoperit cu lipire. Se adoptă un nou proces de sudare prin reflow cu două imprimări cu pastă de lipit: o imprimare cu pastă de lipit, una prin reflow care nu acoperă QFN și așchii goale care descarcă gazul din lipit; Procesul specific de imprimare secundară a pastei de lipit, plasture și reflux secundar este prezentat în Figura 13.
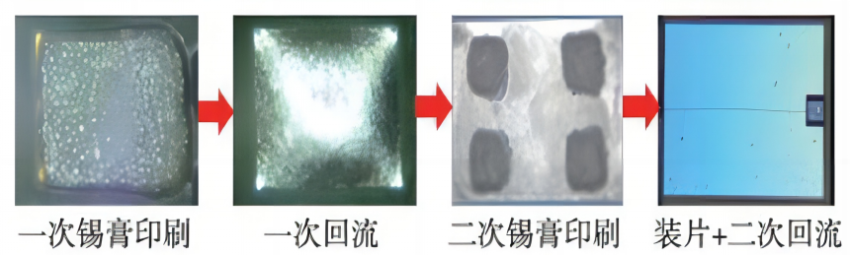
Când pasta de lipit cu o grosime de 75 μm este imprimată pentru prima dată, cea mai mare parte a gazului din lipirea fără capac de cip scapă de la suprafață, iar grosimea după reflux este de aproximativ 50 μm. După finalizarea refluxului primar, pe suprafața lipitului solidificat răcit sunt imprimate pătrate mici (pentru a reduce cantitatea de pastă de lipit, a reduce cantitatea de scurgere de gaz, a reduce sau a elimina stropii de lipit), iar pasta de lipit cu o grosime de 50 μm (rezultatele testului de mai sus arată că 100 μm este cel mai bun, deci grosimea imprimării secundare este de 100 μm.50 μm=50 μm), apoi instalați cipul și apoi reveniți prin 80 s. Aproape că nu există nicio gaură în lipire după prima imprimare și reflow, iar pasta de lipit din a doua imprimare este mică, iar orificiul de sudură este mic, așa cum se arată în Figura 14.
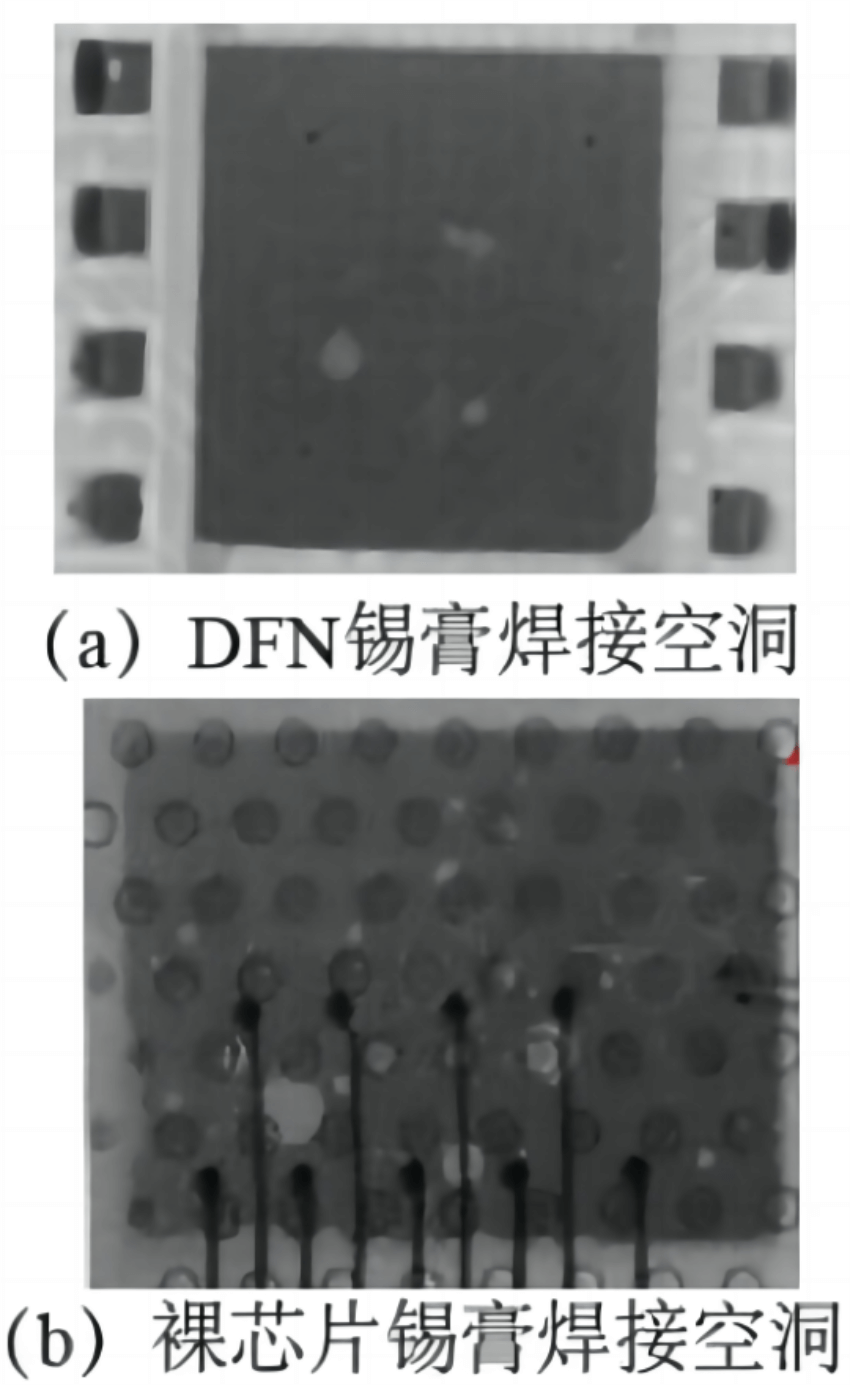
După două imprimări de pastă de lipit, desen gol
4.3 Verificarea efectului cavităţii de sudare
Producția a 2000 de produse (grosimea primei plase de oțel de imprimare este de 75 μm, grosimea celei de-a doua plase de oțel de imprimare este de 50 μm), alte condiții neschimbate, măsurarea aleatorie a 500 QFN și rata cavității de sudare a așchiilor, a constatat că noul proces după primul reflux fără cavitate, după al doilea reflux QFN Rata maximă a cavităţii de sudare este de 4,8%, iar sudarea maximă rata de cavitate a cipului este de 4,1%. În comparație cu procesul original de sudură prin imprimare cu o singură pastă și cu procesul optimizat DOE, cavitatea de sudare este redusă semnificativ, așa cum se arată în Figura 15. Nu au fost găsite fisuri de așchii după testele funcționale ale tuturor produselor.
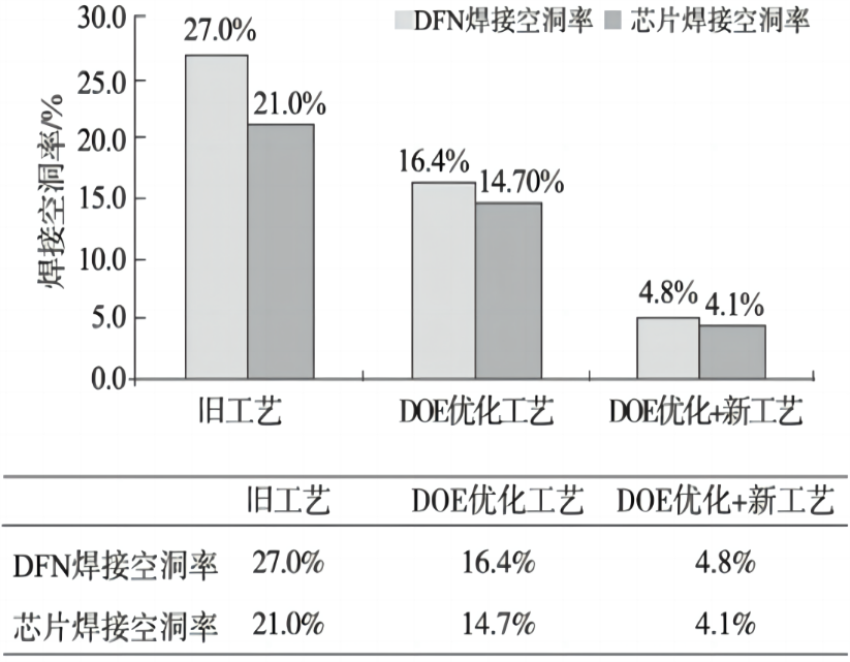
5 Rezumat
Optimizarea cantității de imprimare a pastei de lipit și a timpului de reflux poate reduce zona cavității de sudare, dar rata cavității de sudură este încă mare. Utilizarea a două tehnici de sudare prin reflow prin imprimare a pastei de lipit poate maximiza eficient rata cavității de sudare. Zona de sudare a cipului gol al circuitului QFN poate fi de 4,4 mm x 4,1 mm și, respectiv, 3,0 mm x 2,3 mm în producția de masă. Rata cavității de sudare prin reflow este controlată sub 5%, ceea ce îmbunătățește calitatea și fiabilitatea sudării prin reflow. Cercetarea din această lucrare oferă o referință importantă pentru îmbunătățirea problemei cavității de sudare a suprafețelor de sudare mari.